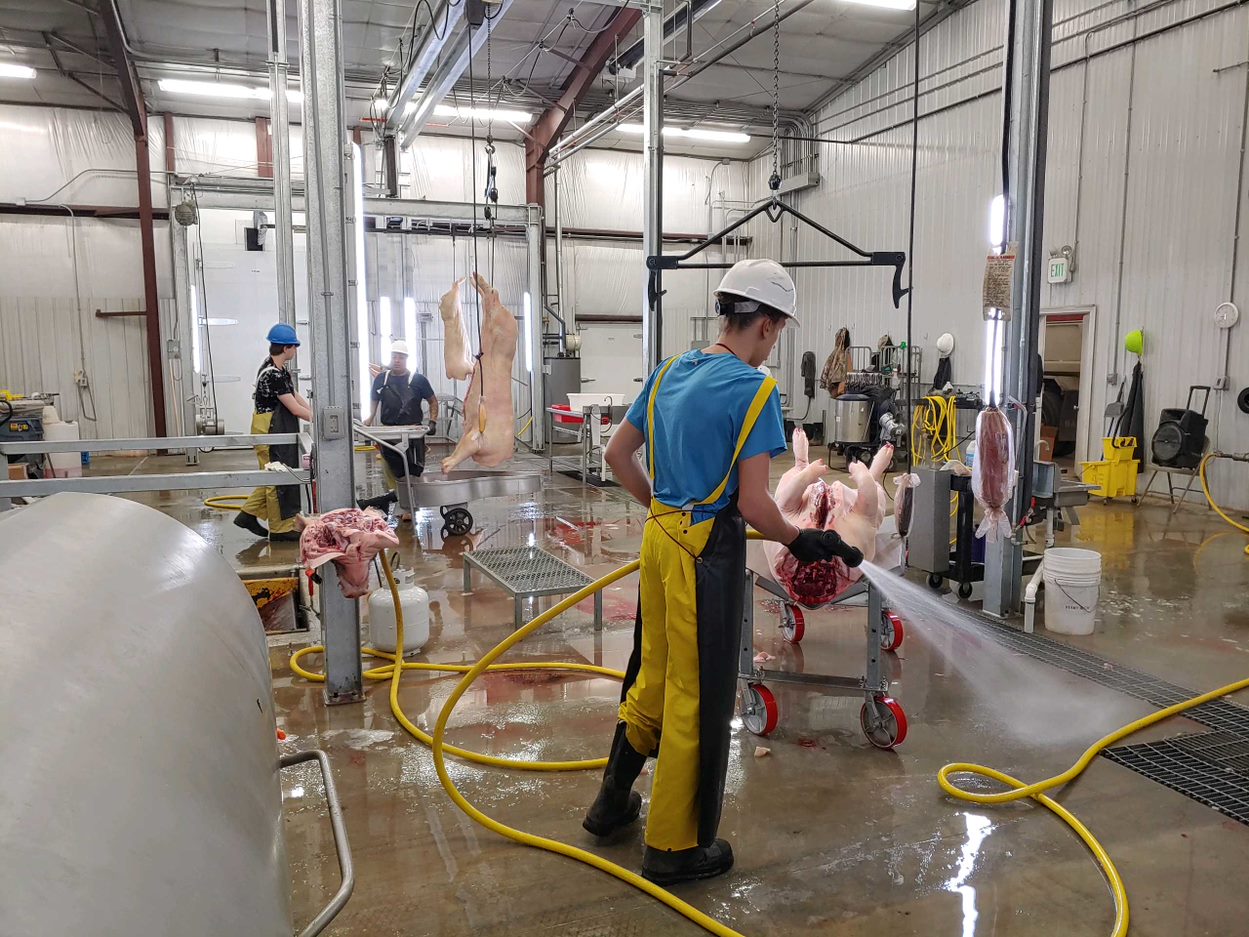
Workers at Callicrate Cattle Co. processing hogs with a new more efficient and humane facility design.
November 1, 2021
Estimated costs for building one large 1,500 head-per-day industrial beef slaughter facility is around 300 million dollars. This is for a plant that would likely fail, as it would be dependent on existing big retailers and food service companies that have, for many years, been purchasing below cost of production meat from their highly predatory big meatpacking partners.
Instead, that same 300 million dollars could be used to build hundreds of smaller cooperative and owner-operated local/regional plants capable of processing between two and six times more total cattle, plus other species of livestock, than one large 1,500 head-per-day mini-Tyson, Cargill, JBS and Marfrig style plants.
Multiple small plants would provide family farmers, ranchers and consumers a far more resilient, sustainable and fair food system with safer, higher quality and more affordable local sources of food. Newly trained butchers and meat cutters could once again practice a valuable and respectable trade, earning living incomes in better designed, more productive, and safer workplaces.
The smaller, more efficient, and reliable multi-species plants providing services and markets to livestock producers able to earn more of the consumer dollar, would keep wealth and kids in the community and build important farm-to-plate-rural-urban connections, while improving food security, animal welfare, and the environment.
Whole animal butcher shops with access to fresh carcasses could once again profitably serve the specific needs of communities, instead of supporting corporate interests by buying untraceable, boxed meat from members of the multinational meatpacker cartel.
—————-
Please explain: “Instead, that same 300 million dollars could be used to build hundreds of smaller cooperative and owner-operated local/regional plants capable of processing between two and six times more total cattle, plus other species of livestock, than one large 1,500 head-per-day mini-Tyson style plant.”
According to Tyson’s reporting on capacity and labor force at their largest plants, Dakota City, Nebraska and Garden City, Kansas, they are processing less than 1.6 cattle per day per employee.
Small owner-operated plants are typically able to process somewhere around four head per man per day with a more skilled and stable workforce. This is where the 2x comes from. One small plant I’m familiar with consistently processed ten head per highly-skilled worker with a simple and inexpensive cradle system. Prior to going out of business, the plant expanded to an expensive overhead moving rail system with a mechanical hide puller and production per worker was cut basically in half.
The mobile slaughter unit (MSU) that just arrived in Montana last week is capable of processing a beef animal every twenty minutes with four skilled workers. The cooler has a capacity of between 15 and 18 head depending on animal size. A quartering and docking section extends rearward from the cooler, providing a space outside the cooler for quartering, increasing daily capacity by making more room inside the cooler for hanging the half carcasses. The MSU cooler is emptied at the beginning of each day, either into a holding cooler or onto a carcass transport trailer or truck, where the carcasses are shipped to our cut facility in Colorado Springs.
Prior to selling the above MSU, Callicrate Cattle Co. constructed a building to house the unit for all weather operations with intentions to eventually move the unit out, constructing a kill floor with an attached cooler, including a thirty head drip side and forty head finish and holding area. This increased kill capacity to thirty head per day with additional labor.
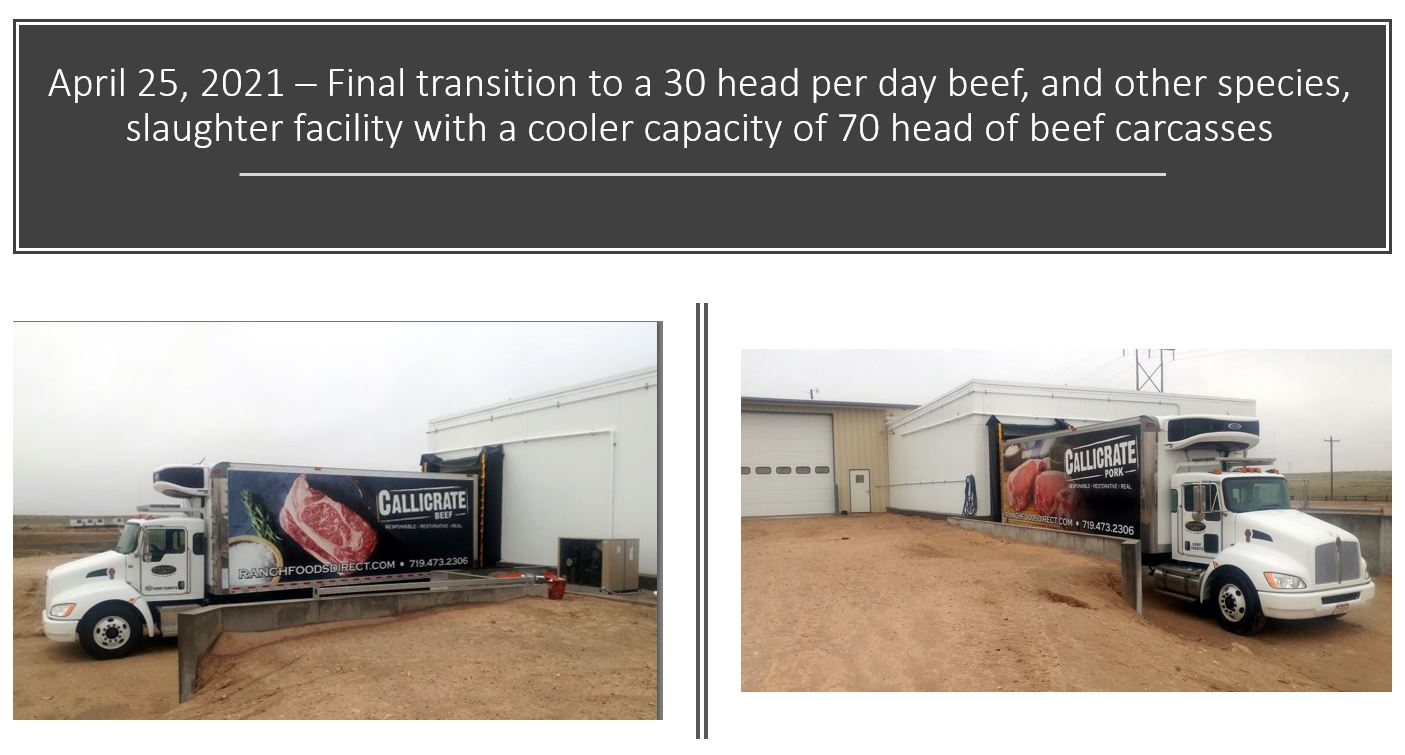
The new carcass cooler attached to the existing building allows for increased processing by adding carcass holding and aging capacity prior to transporting to Colorado Springs for further processing for our retail and wholesale markets.
The above facilities cost between a one-third of a million for the MSU, and nearly one-million dollars for the permanent purpose-built facility to manufacture and construct. Three hundred thirty-head per day plants, costing one million dollars each, would provide a processing capacity for 9,000 head per day, hence the 6x number. It’s also important to know that the small plants are single shift, unlike the big plants that run two kill shifts and one cleanup shift.
As with the large plants, the MSU and small slaughter facilities don’t process to retail cuts. For many years, big retailers and food service, along with their big meatpacker partners have been shutting out competitors and cooperating in reducing the cost of livestock and labor, as well as externalizing many other costs onto the public with captive supplies and boxed beef being the major market wrecking weapons. Cattle producers have lost over 30% of their share of the consumer beef dollar due to this abusive market power and labor has lost a living wage and a humane workplace. It is critical in building new local/regional food systems to develop markets for carcasses once again. We need many more carcass processing facilities combined with whole animal retail butcher shops like we have in Colorado Springs.
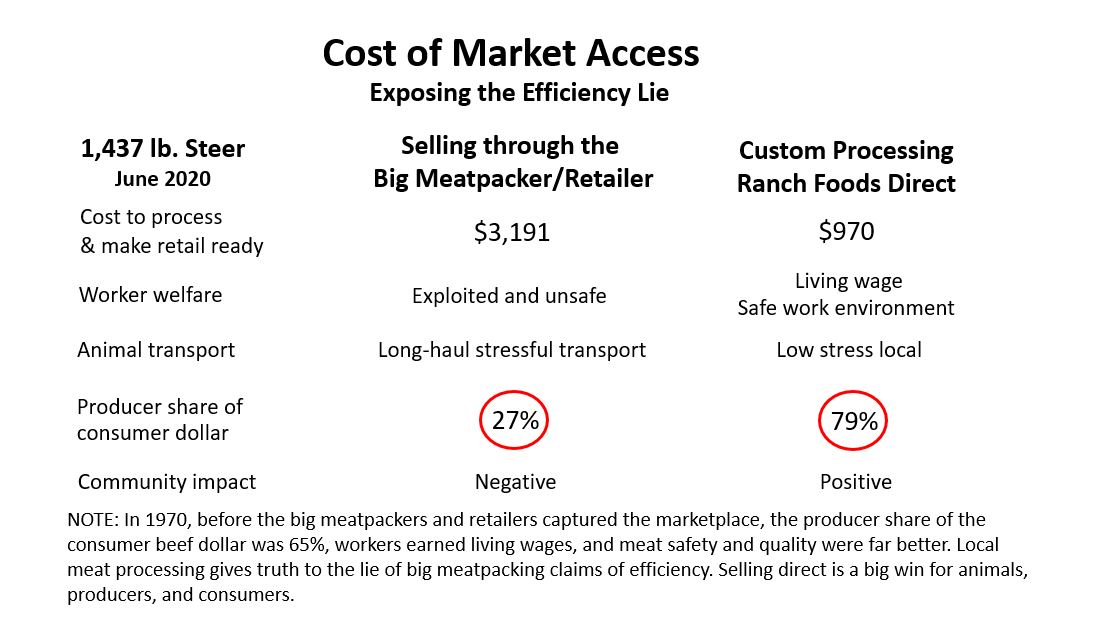
Big meatpacking’s real efficiency is in their ability to extract wealth from both the producer and consumer.